A good maintenance plan should always include routine stretch wrap machine repair.
A good maintenance plan should always include routine stretch wrap machine repair.
Blog Article
Recognizing the Significance of Timely Stretch Cover Equipment Repair Service Solutions
When it pertains to stretch cover devices, prompt repair services can make all the difference. You recognize that even small mechanical or electrical concerns can cause unexpected downtime, influencing your assembly line. Resolving these issues promptly not only maintains efficiency yet also improves the quality of your covered items. What factors should you take into consideration to guarantee your makers remain in leading shape? Allow's discover this essential element better.
The Function of Stretch Cover Machines in Modern Manufacturing
Stretch cover equipments play a necessary duty in modern-day manufacturing by guaranteeing that items are firmly packaged for transport and storage. You count on these machines to offer security and security, stopping damages throughout transit. When you use stretch wrap, you reduce the danger of products changing or obtaining crushed, which can bring about pricey losses.
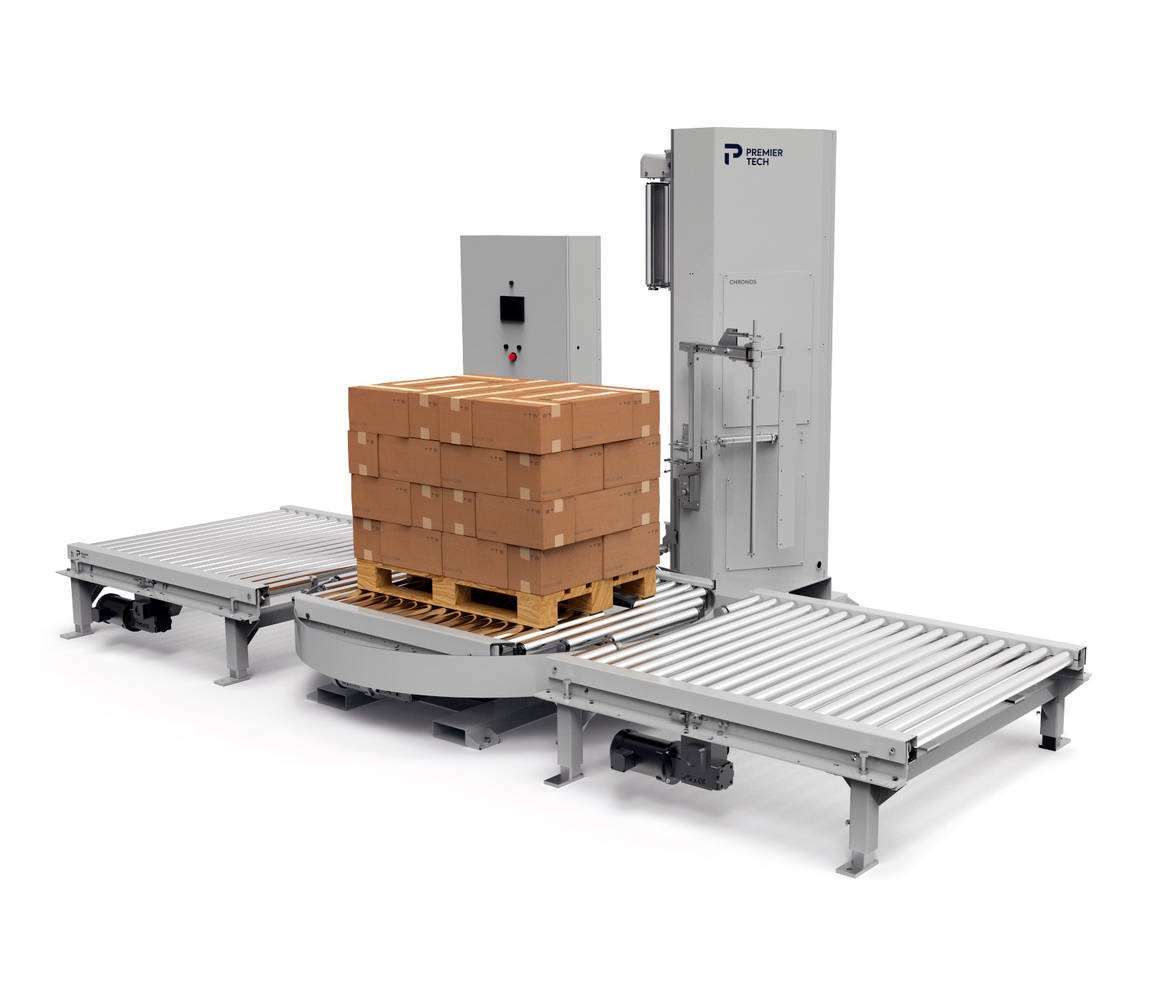
In addition, making use of stretch wrap equipments can boost your overall supply chain efficiency. By enhancing the product packaging procedure, you minimize labor prices and quicken delivery times, making certain that your consumers get their products without delay. In today's hectic market, this advantage is vital.
Usual Concerns That Cause Device Downtime
When your stretch wrap machine experiences downtime, it can commonly be traced back to mechanical failings or operator errors. Recognizing these common issues can aid you stop costly interruptions. By addressing these factors, you can maintain your procedures running efficiently.
Mechanical Failures and Break Downs
When parts put on down or break, your stretch cover machine may halt unexpectedly, affecting efficiency. Furthermore, electric failures can cause breakdowns in the equipment's control system, developing further delays. By focusing on prompt repair work, you're not just decreasing downtime but additionally prolonging the life-span of your equipment.
Driver Errors and Oversights
While operators play an important role in the smooth functioning of your stretch cover equipment, their errors and oversights can lead to substantial downtime. Usual issues like incorrect loading, inaccurate setups, and failure to monitor wrap tension can trigger delays and item damages. For instance, if an operator neglects to inspect for worn-out movie, it can result in irregular wrapping and raised waste. Furthermore, miscommunication throughout changes can result in vital adjustments being neglected. It is very important to offer complete training and routine refresher courses to minimize these errors. Urging a society of liability and vigilance amongst your team can substantially minimize downtime. Ultimately, buying driver training repays by improving performance and extending your machine's lifespan.
The Financial Influence of Delayed Repairs
Delaying repairs on your stretch cover maker can lead to significant financial consequences that ripple via your whole procedure. When your machine breaks down, productivity plummets.
Furthermore, extended hold-ups can escalate small issues into significant troubles, calling for a lot more considerable repairs or even total substitute of the device. Ultimately, timely repair services are necessary to keeping your bottom line and making certain smooth operations.
Advantages of Proactive Maintenance Programs
Prompt fixings can save you from pricey downtime, however executing an aggressive maintenance program takes it an action additionally. By on a regular basis setting up maintenance, you can identify potential concerns before they rise right into significant problems. This not only maintains your stretch wrap machine running efficiently however likewise extends its life-span. You'll locate that consistent upkeep decreases the likelihood of unforeseen malfunctions, allowing your procedures to run much more effectively.
Moreover, an aggressive approach improves efficiency. With fewer disruptions, your labor force can concentrate on their tasks without the stress of abrupt device failures. Plus, you'll likely minimize repair expenses, as small concerns are usually less expensive to repair than considerable repairs. Finally, maintaining peak performance can enhance the top quality of your covered products, ensuring customer fulfillment. In the lengthy run, a proactive maintenance program is a financial investment that settles via increased reliability and cost savings.
Identifying Indicators That Your Equipment Needs Repair
As you operate your stretch wrap device, it is important to stay vigilant for indications that indicate it might need fixing. Among the initial points to try to find is unusual noise. If you listen to grinding, squealing, or any various other strange audios, it can signify a hidden issue. In addition, expect inconsistent covering. If the movie isn't adhered effectively or you observe irregular stress, your maker might be malfunctioning.
One more indication is a rise in downtime. If your device regularly quits or calls for changes, it is time to explore. Also, watch on the maker's speed; if it's slower than common, something may be incorrect. Finally, any visible damage like torn cable televisions or leakages need to not be overlooked. Quickly dealing with these signs can avoid a lot more considerable issues down the line, ensuring your procedures run efficiently.
Picking the Right Repair Work Service for Your Demands
Exactly how do you pick the best repair work service for your stretch cover device? Look for service technicians who specialize Going Here in stretch wrap equipments and have a tried and tested track document.
Next, examine their response time. A reputable service ought to use timely assistance, as equipment downtime can be pricey. It's also vital to understand if they offer emergency situation fixings.
Do not neglect to ask regarding service warranties on repair work and components. A trusted solution supports their job, offering you comfort.
Lastly, compare rates however stay clear of choosing solely based on cost. Sometimes, the least expensive alternative may lead to substandard solution. By considering these elements, you'll discover a fixing solution that meets your demands and maintains your stretch wrap device running efficiently.
Methods for Minimizing Stretch Wrap Maker Downtime

Training your operators is an additional essential strategy. Equip them with the knowledge to recognize and deal with small glitches before they bring about considerable failures. Encourage them to maintain a log of any type of abnormalities, which helps in identifying issues faster.
In addition, preserving a supply of necessary spare parts can drastically lower downtime. When something breaks, having the ideal parts on hand implies you won't have to wait for shipments.
Lastly, consider purchasing real-time tracking systems. These systems can signal you to performance changes, enabling for prompt intervention. By applying these strategies, you'll keep your stretch wrap maker running smoothly and successfully.
Frequently Asked Questions
Exactly How Usually Should Stretch Cover Machines Be Serviced?
You need to service stretch wrap devices on a regular basis, preferably every six months. However, if you discover any type of efficiency issues or unusual sounds, don't wait-- timetable maintenance immediately to avoid costly failures and guarantee peak performance.
What Are the Typical Expenses Associated With Stretch Cover Maker Services?
Typical expenses for stretch cover device fixings vary, however you might expect to invest Clicking Here between $200 to $1,500 depending on the issue. Regular maintenance can help minimize these prices and expand your device's life-span.
Can I Carry Out Basic Upkeep on My Stretch Wrap Machine?
Yes, you can do fundamental upkeep on your stretch wrap maker. Regularly inspect for damage, clean the parts, and guarantee appropriate lubrication. Maintaining it healthy can expand its lifespan and improve efficiency.
How Do I Know if a Repair Work Service Is Reliable?
To discover a reliable repair solution, check on-line evaluations, ask for referrals, and confirm accreditations. A dependable service will certainly give clear quotes, guarantee choices, and prompt communication, ensuring you really feel confident in their competence.
What Should I Perform in Case of an Emergency Situation Maker Breakdown?
In instance of an emergency situation maker failure, you should right away quit operations, assess the problem, and call your repair solution. Maintain essential contact numbers convenient, and record the problem for efficient troubleshooting when assistance gets here.
Verdict
To go to this web-site summarize, understanding the value of prompt stretch wrap maker repair services can significantly improve your procedures. By attending to problems promptly, you reduce downtime and avoid pricey breakdowns. Embracing aggressive maintenance not only expands your devices's lifespan yet likewise enhances efficiency and consumer satisfaction. Bear in mind to stay cautious for signs of wear and pick a dependable repair service to keep your machines running efficiently. Spending in these options pays off in the future, ensuring your supply chain continues to be reliable and effective.
Report this page